Best ERP Software for Brewery Business in India
ERP Software for Brewery Manufacturing Industries
At Tech Alphonic we Best ERP Software for Brewery Business in India for your businesses because we understand that each manufacturing operation is unique. Our ERP systems are custom-built according to your business needs with our expert help and support. We can make your business run smoothly. Our developers have 7+ years of experience building software to enhance your business. Get connected with us today!
Manufacturing ERP Software for Breweries
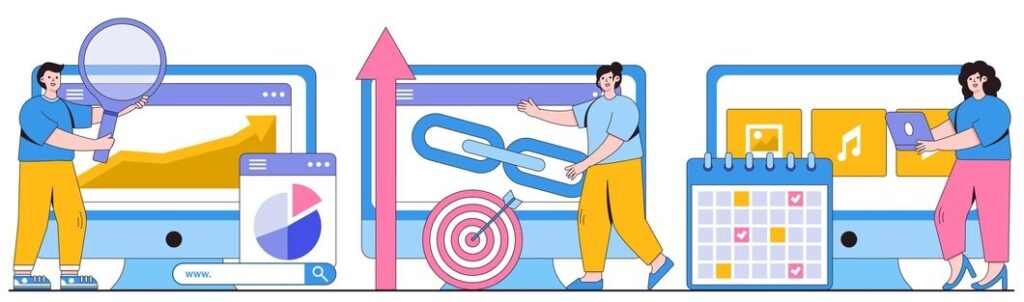
What is the brewery industry?
As breweries continue getting larger and the demand for craft and speciality beers increases, efficient management of such operations could easily result in lost revenue and compliance problems in manual management. This is where ERP software comes in handy by providing a single application through which all the dispersed functions together will help in streamlining, automating, and enhancing every aspect of brewery management.
Why Do Breweries Need ERP Solutions?
ERP system is a combination of integrated tools meant for managing, observing, and optimizing the activities of multiple functions in the brewery, including manufacturing, quality assurance, inventory management, sales, distribution, and financial reporting. Those are some of the core reasons
why breweries benefit significantly from ERP solutions: Some of the compliance requirements through rules and regulations include food safety, quality of production of liquor, methods of liquor distribution, and labelling by the brewery. The ERP system ensures it complies with the requirement by managing tracking for compliance on all the production processes to avoid expensive penalties for the violation of laws.
Inventory and supply chain management: It is the source of raw ingredients for brewing because of which the brewery needs to depend on the availability and quality of the raw ingredients for their production. Poor inventory management leads to delays in manufacturing or spoilage of the ingredient. This is where ERP software shows the stock level in real-time, and simplifies the procurement process while minimizing the risks of stock out or excess stock.
Brew Production Scheduling and Optimization: The brewing process has stages that include mashing, and fermenting, among others that make management hard, especially when production takes place on several beer varieties. ERPs will enable the breweries to efficiently plan their cycles of production and optimize schedules for brewing, monitor progress, and meet the needs in production without compromising quality.
Â
ERP Features-Critical to the Alcohol and Distillery Business
Management of Production: Tune the production to cater to regulated needs by the distillery. Track the production process to ensure each constituent in fermentation, distillation, and ageing is documented in detail. Data is captured directly from machines to give timely updates and maintenance alerts, all through integration with IoT devices.
Quality Management: Automated quality checks for production and post-production. Compliance with industry-specific certifications such as ISO and HACCP, including audit documentation. Enhanced traceability for the ingredient batches to quickly identify problems in case of product recall.
Inventory and Supply Chain Management: Real-time tracking and forecasting of ingredient requirements, thereby avoiding shortfalls and excesses. Integration with suppliers and distributors for easy procurement, getting materials at the right time Warehouse management software to manage free spaces, and prevent spoilage based on expiration dates.
Brew Production Scheduling and Optimization: The brewing process has stages that include mashing, and fermenting, among others that make management hard, especially when production takes place on several beer varieties. ERPs will enable the breweries to efficiently plan their cycles of production and optimize schedules for brewing, monitor progress, and meet the needs in production without compromising quality.
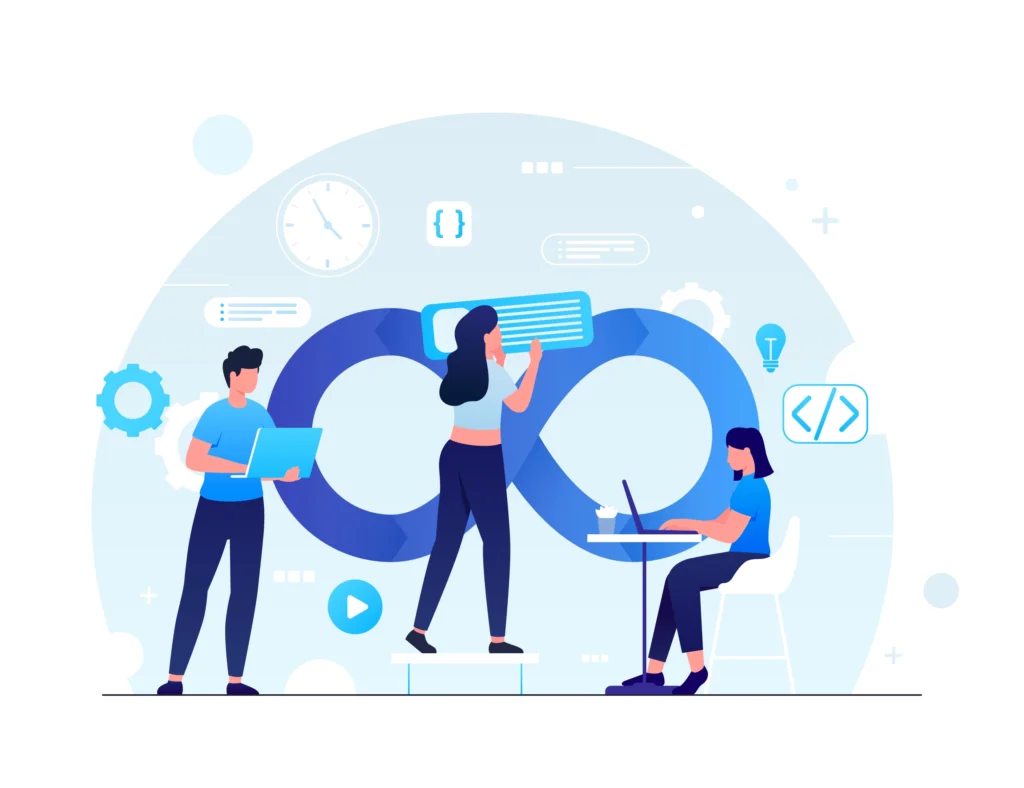
Quality Assurance and Traceability: Quality is the difference between a brewery and a brew-fermentation facility. Quality deviations result in dissatisfied customers and, therefore, lost sales. ERP systems ensure constant quality through the capture of quality checks, testing results, and traceability from raw materials all the way to the final product.
Sales and Distribution Management: Proper orders and distribution management are the most important steps followed to satisfy the customers of the brewery. It makes the process of order processing easier, tracks shipments, supports distribution planning, and hence easy management of their sales channels for timely delivery.
Main Features of Brewery ERP Production and Recipe Management: NULL Actual real-time brew stage tracking: temperature, pH, and other key factors affecting the quality of the beers, coupled with alert capabilities. Tools to prepare well for peak production periods through demand data prediction and reduction of scrap and unpreventable downtimes through efficient utilization of equipment.
Quality Management: Automated quality control at every step from material testing to final tasting of the beer. Certification in compliance with Food Safety through HACCP and ISO. Traceability capacities, keep track of each batch of ingredients so that in the event of a product being segregated due to a recall, can quickly locate the batches.

Development that
Drive Sales & Brand Recognition
A well-designed and user-friendly website builds brand trust and creates a lasting positive impression on your customers. We’re an award-winning digital marketing company & Social Media agency in New Delhi India. We offer 360°digital solutions that enrich your online presence.
Inventory and Procurement Management: The raw material and ingredients would be tracked suitably in time, reducing losses since orders would be available when the ingredients would be needed thereby retaining their freshness. Customer management for the procurement process to monitor the performance of suppliers better, which means that a brewery would easily acquire new raw materials at cost-effective prices It aligns well with the IoT-enabled sensors monitoring the conditions under which ingredients are kept such as temperature and humidity levels that always come with adverse effects on the quality of the ingredient.
Sales, Distribution, and Customer Relationship Management (CRM): Automate order processing linking it to sales data with production and stock, and prevent overproduction to try to meet the brewing demand. CRM integration for management of relationships between distributors, tracking of orders from customers, and analysis of sales trend Tools in distribution planning that allow coordination of delivery schedules, manager shipping costs, and compliance with regional distribution laws.
Financial and Compliance Management: Automated financial tracking and reporting to manage the budget of breweries understand revenue, and control costs. Compliance management to standardize excise tax calculations, licensing, and other aspects of regulatory compliance. Real-time financial insights to help breweries understand profitability, cost of production, and support plans for future growth. Implementing ERP in breweries – how?
This will automatize repetitive chores because one of the major inefficiencies dealt with in ERP implementations is the elimination of manual reporting and data entry for personnel. In that case, teams are freed up to focus on more valuable activities such as optimizing recipes, improving productions, or bettering relationships with customers. Increased decision-making with data insights: The availability of real-time data and analytics enables breweries to make far more relevant decisions regarding their production schedules, levels of inventory, pricing, and promotions. In this manner, the brewery is proactive and reactive to market trends and customer preferences.
Better Compliance and Less Risk: The ERP systems ensure that compliance is incorporated into every aspect of the brewing process, thus ensuring reduced risks from non-compliance and possible penalties. Breweries can demonstrate compliance in case of inspection and audit through this documented evidence.
Potential Cost Savings through Inventory Optimization: Real-time inventory tracking would save on cost wastes as well as overstocking. Accurate estimation of demand will allow breweries to have an effective production plan, which reduces space and holding costs.
Better Customer Satisfaction: ERP provides catch-up with the demands, avoiding stockouts, and delivering appropriate orders on time. Consistent high quality shall help build trust and loyalty among the customers.
ERP System Implementation: Key Considerations for Breweries While breweries consider the implementation of an ERP system, several considerations must be kept in mind to make it the best fit for their requirements
Specificity and Flexibility: Depending upon every brewery, it would be a different process, recipe, and market requirement. An ERP system that is customizable would be required for the specific production needs of any business as well as any future expansion.
Scalability for Growth: The system should be capable enough to withstand higher production volumes, the introduction of new product lines, and a more comprehensive distribution channel without significant revamps or overhauls as the brewery goes through its growth process.
Implementation from an experienced vendor in brewing: An implementation from a vendor that understands the brewery industry and its specifics will greatly ease the implantation process. Such vendors could sensitize and calibrate the system with such industry-specific demands as a result.
User Training and Support: True adoption from the users is needed to get maximum returns after the implementation of an ERP system. Breweries should involve themselves with their ERP provider and then train their employees adequately and ensure continuous support in case there is a technical glitch or updates.
Data Security and Compliance: As very sensitive financial and operational data are housed in ERP systems, solutions with high security and good access controls, data encryption, and regular gradation of systems should be targeted by breweries.
Why choose us?
Customized Solutions:
Every manufacturing operation is unique, and we know that. Our ERP systems are customized to suit your processes, goals, and workflows, which guarantee the highest efficiency.
Industry Expertise:
Our team has vast experience in the field of manufacturing ERP solutions, which gives them the technical know-how and industry insights that would be able to solve the common challenges and best practices that should be implemented.
Integration
Our ERP solutions get seamlessly integrated with your current systems (inventory, supply chain, CRM) in order to build a cohesive, unified platform that enables you to conduct operations on a more streamlined basis.
Cost-Effective and Scalable:
We offer scalable ERP solutions that can grow along with your business and give you long-term value without compromising quality or performance.
Quality control is the core of our development process. In-depth testing of the system ensures that the ERP system is stable, efficient, and fully functional at the launch time.
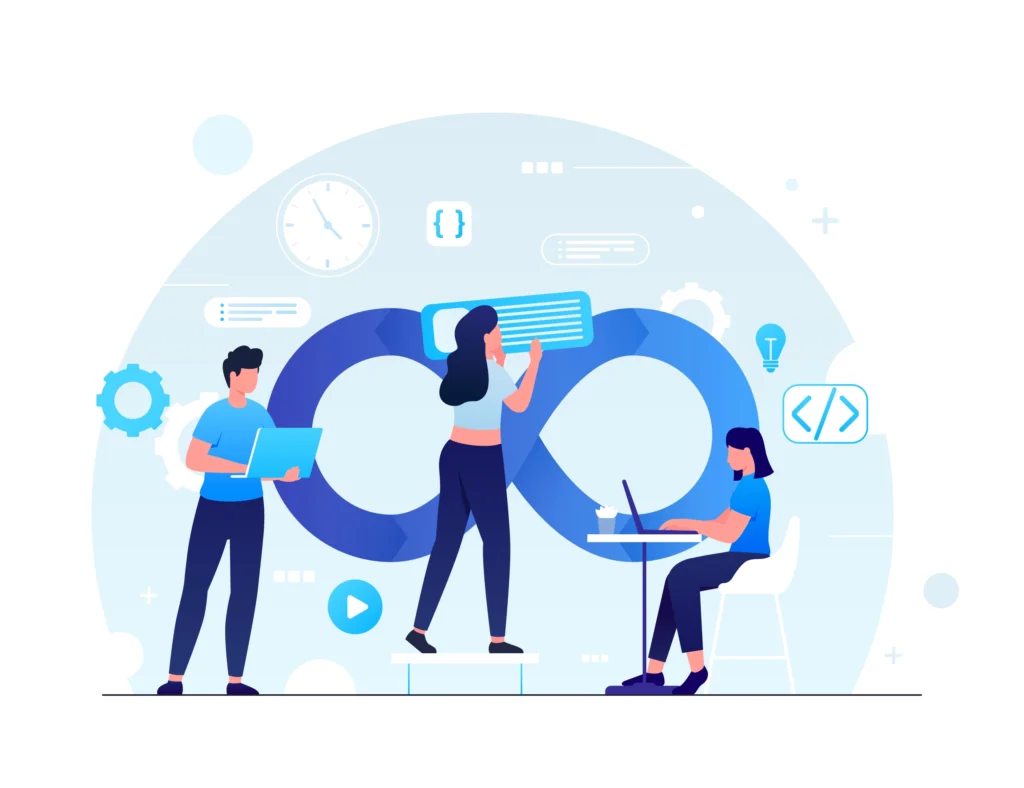
We start by comprehending your business objectives, target audience, and specific needs. This allows us to gather valuable insights that will guide the development of your ecommerce website.
Our expert team creates a customized strategy for your ecommerce website, detailing key features, functionalities, and design elements.
Our professionals transform ideas into stunning visuals and user-friendly layouts, optimizing for speed, efficiency, and search engine visibility.
We rigorously test across devices and browsers, incorporating your feedback to ensure a seamless user experience and an exceptional website.
Our commitment doesn't end with the launch of your ecommerce website. We offer comprehensive support and maintenance services to ensure your online store remains secure.
Working Process
Our Strong working
process
At Tech Alphonic, we’re obsessed with delivering exceptional results. We achieve this through a laser-focused, detailed process that streamlines every step of your project. Think of it as a well-oiled machine – efficient, on-time, and built to deliver exactly what you need. We take pride in keeping your project within budget and exceeding your expectations.